液冷型高功率动力电池包冷却性能研究
罗仁宏 杨景泉 李如平 朱流群
摘 要:为解决某新能源车液冷型动力电池包在50C高倍率放电工况下温升过快和温差较大问题,提出了5种电池包液冷板水管改进方案,并采用仿真结合试验的方法对电芯模组温度云图、最高温度、最大温差以及平均温度等结果进行对比分析,分析结果显示改进方案5的冷却效果最佳,其最高温度为40℃,最大温差为10.7℃,均优于其它方案,满足电芯模组冷却要求。可为提升新能源车高功率动力电池包冷却性能提供方法借鉴。
关键词:高功率电池包;液冷板;冷却性能;仿真结合试验
引 言
随着能源紧缺和人们对环境保护意识的日益增强,开展节能环保的新能源电动车已经成为世界各国研究的重点。而动力电池作为电动车唯一的动力源,其性能优劣直接决定了汽车安全性、动力性和续航里程。
动力电池对温度要求十分严格,其最佳工作温度一般都在20~50℃左右,电池温度过低,会导致电池电容降低,过高则会导致电池组可能会出现液漏、起火以及爆炸等安全事故。同时,考虑到较大的温差会导致单体电芯的一致性,从而使电池模组电池性能下降更为严重,因此对于单体电芯或者电芯模组温差应控制在10℃以内。
设计高效的电池冷却系统,对动力电池进行高温冷却、低温加热以及保温等功能,从而实现电池温度均匀性,确保电池处于最佳工作环境下,保障了电动车安全性和整车动力性能。
按照动力电池包冷却介质分类,可以分为风冷、液冷、热管、相变材质冷却方式。Rui Liu等分析了液冷、相变材质和风冷冷却效果,分析结果表明液冷冷却效果高于相变材质冷却,风冷最低。Yuan等通过对比不同电池包冷却方式,得到间接液冷比直接液冷效率更高。可见,动力电池包液冷是未来电池热管理研究的方向以及应用的热点。
本次研究是基于自主研发的新型动力电池包在50C高倍率放电过程中,出现电池温升过高和温差过大的问题,为了使电芯最高温度不超过42℃、电芯模块最大温差不超过10℃,以该单体电芯发热为研究基础,首先将单体电芯在50C倍率放电工况下电芯表面温度计算值与实验值对比分析,从而验证计算模型的可靠性。设计了5种不同布置位置的液冷板对电芯模块的冷却效果影响,利用数值计算探究了在50C高倍率放电工况下各方案的散热效果,得出了影响高倍率下电芯模组散热效果的因素和最佳冷却方案。最后,对方案5进行实验测试,计算值与实验值相吻合,验证了方案5的有效性,为电池包热管理开发设计提供借鉴。
一、计算模型搭建和标定
1.电芯生热原理
由于磷酸铁锂电池的实际生热情况十分复杂,Bernardi等提出单体电芯生热计算模型,如下公式
(1)
其中I和R分布为电芯的电流和内阻,Vb是单体电芯的体积,Tb是单体电芯的温度,电芯内阻可以通过实验HPPC在SOC下获得。导热材质、水冷管、单体电芯和冷却介质等主要热物性参数如表1所示。
表1 电芯模块物理参数
项目 |
数值 |
单位 |
电芯 |
电芯密度 |
1646 |
Kg/m3 |
电芯比热容 |
1118 |
J/Kg*℃ |
电芯热传导系数 |
X: 20 |
W/m*k |
Y: 20 |
Z: 2 |
冷却液 |
动力粘度 |
0.00339 |
Pa-s |
密度 |
1071 |
Kg/m^3 |
冷却液热传导系数 |
0.384 |
W/m·k |
冷却液比热容 |
3300 |
J/kg*℃ |
导热垫 |
密度 |
1200 |
Kg/m3 |
导热系数 |
2 |
W/m·k |
比热容 |
1700 |
J/Kg*℃ |
冷板 |
密度 |
2702 |
Kg/m3 |
导热系数 |
237 |
W/m·k |
比热容 |
903 |
J/Kg*℃ |
2.计算模型的标定
利用计算软件对高倍率(50C)下电芯模组散热进行瞬态分析,计算模型采用的层流换热模型,进、出口分别采用质量流量界面和压力出口界面,电芯表面换热系数设为2W/(m2*k),单位时间步长迭代20次,时间步长为0.01s,能量计算采用的是二阶精度。将电芯单体简化成长宽高分别为308mm、10mm和103mm的长方体,计算区域采用六面体网格和薄面体网格,并对电芯附近层的网格加密,网格总数为1200万。
磷酸铁锂电芯的50C高倍率放电特性试验平台如图1所示,实验前,先将电池充满电,并对其表面布置有热电偶传感器,精度为0.1℃,温度传感器布置位置如图1(c)所示;然后置于27℃的恒温恒湿的试验箱里不少于2个小时,从而确保电芯内外温度一致;最后,对电池组进行50C放电试验,持续时间为15S,并记录测试点温度值,重复3次,最后取其平均值。
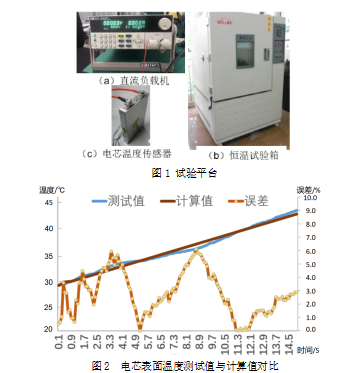
图2是电芯在放电过程中被检测的电池表面平均温度实验值与计算值的对比结果,从图中可以看出,两者变化趋势基本吻合,计算值与实验值的最大差值不超过2.4℃,最大误差不超过7%,从而验证了本次仿真计算的有效性。
二、液冷板布置设计
原始方案是在电池块的两侧布置液冷板,液冷板的厚度为10mm,前后两端面液冷板厚度为2mm,水管的布置形式如图3所示,水管的直径为6mm,进水量为0.14L/min。
对原始方案进行分析,综合考虑了冷却效果、制造工艺和成本,提出了5种液冷板水管布置方案,每种改进方案的电池模组总进水流量为定值,具体改进方案如下:
方案1液冷板的布置形式如图方案2所示,将两侧S型水管改成5根支路直流水路,每根支路水冷管的直径为6mm,支路水冷管的进水量为0.028L/min。
方案2是在电池的上下两面都布置微型液冷板,厚度为4mm,其液冷板内水路的走向如图所示,水管截面为2*2mm的口琴管,一共布置6层液冷板,每一层支路水管的进水量为0.47L/min。
方案3是结合方案2和方案1的综合体,每根支路进水量为0.0175 L/min。
方案4是在方案3的基础上,改变微型液冷板中水路的走向,如图所示。
方案5是设计了10根S型水路穿插在电芯之间,如图3所示,每根支路的进水流量为0.014L/min。
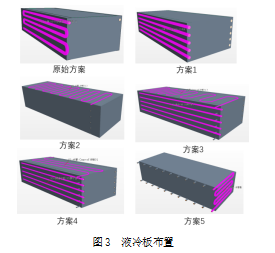
三、结果分析
1.电池模块温度云图分析
图4可以看出,原始方案和方案1都出现了明显的积热问题,主要原因是因为电芯在放电过程中,电芯的热量主要由中间向四周传热,由于持续时间短,发热功率高,从而电芯两侧的液冷板无法快速的带走电芯中心处多余的热量,从而造成电芯中心部分的温度快速上升。
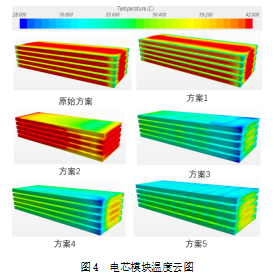
方案2是在电芯之间布置微型液冷板,从计算的结果可以看出,电芯中心处的热量出现明显的降低,但电芯的四周温度还是无法有效地带走,从而电芯四周的温度依然很高。
方案3是综合了方案1和方案2,由于电芯上下面和两侧都布置了液冷板,从而使得电芯的温度能快速下降,但可以看到,进水口处电芯的表面温度较低,而出水口处的电芯表面温度相对较高,电芯表面温度的均匀性也不是很理想。
方案4是在方案3的基础上,改变了微型液冷板的水路走向,从温度云图可以看出,进水口处的电芯温度依然相对较低,同时电芯的前后端面都出现不同程度的积热现象。
从方案5的温度云图可以看出,电芯模块温度的均匀性很好,主要是因为S型水路穿插在电芯之间,增大了与电芯表面的接触面积,从而使得每个电芯都能得到充分的散热。
表2 不同方案设计温度对比表
设计方案 |
最低温度/℃ |
最高温度/℃ |
最大温差/℃ |
原始方案 |
29.0 |
47.2 |
18.2 |
方案1 |
30.5 |
46.8 |
16.3 |
方案2 |
33.6 |
47.2 |
13.6 |
方案3 |
28.2 |
41.6 |
13.4 |
方案4 |
27.9 |
42.0 |
14.1 |
方案5 |
29.3 |
40.0 |
10.7 |
为了对各个方案结构的冷却性能做进一步量化分析,提取了每个方案下电芯模块中最低、最高温度和最大温差的数据,如图表2所示。从表2中可以看出,方案5的电芯模块温差最小,并且模块中的最高温度也最低,具有很好的散热性能,这与前面分析一致。
2.电池模块表面积温度占比分析
为了进一步分析出各方案散热性能,对该电芯模块表面的温度分布占比进行对比分析,如图5所示。对电芯表面积进行温度积分,能得到电芯模块单位面积上温度的大小,从而来衡量各个方案的冷却效果。



从图中可以看到,原始方案、方案1和方案2主要分布在39℃到47℃附近,并且温度分布很广泛,电芯的温度均匀性较差;而方案3、方案4和方案5主要分布在35℃附近,并且温度分布较为集中。
从方案1和原始方案的对比,以及方案3和方案4的对比,可以发现它们的表面温度积分和平均温度值都很接近,但标准方差有很大的区别。在只改变了液冷板中水管的走向布局时,能在一定程度上改善电芯模块的温度均匀性,但散热性能的改变不是很明显。
方案4与方案5对比,可以看到方案4的标准偏差最低,说明了温度的均匀性相对较好,但表面温度积分和平均温度都高于方案5。综合考虑,可以得到方案5的冷却性能最好,这与前文分析一致。
3.试验验证
为了验证本次研究方案的准确性,对方案5试制样件,如图6所示,外壳为黑色铝制冷板,电芯固定在其内,铝制冷板中的水管如图3中方案 5所示,穿插在电芯之间。三个测点如图标识所示,分别布置在冷板水管进口处、电芯中心处。整个实验是在高低温环境箱内进行,环境温度始终保持为27℃。
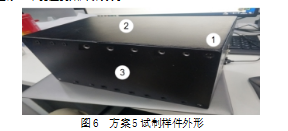
首先,电池充满电后静置在27℃的高低温环境试验箱内2h,从而保证电芯模块温度与环境温度一致性,然后打开水泵,让冷却液开始流动的同时,以50C高倍率放电15S,并记录测试点温度值,重复3次,取其平均值。
表3 实验值与计算值对比分析
名称 |
实验值/℃ |
计算值/℃ |
误差/% |
测点1 |
32.4 |
30.5 |
5.8 |
测点2 |
34.9 |
32.5 |
6.9 |
测点3 |
36.1 |
34.9 |
3.3 |
将实验值与测试值进行对比分析,如表3所示,可以看到计算值与实验值基本吻合,最大误差不超过6.9%,验证了方案5设计的有效性。
四、结论
单体电芯计算值与实验值对比误差均在9%以内,验证了本次计算模型的可靠性,这对电芯模块冷却系统地开发设计具有指导意义。
在其他条件不变情况下,通过改变水管走向布置,能在一定程度上改善电芯模块的温度均匀性。同时不同位置的液冷板对电芯模块散热性能有很大的影响。
在总进水量不变的情况下,对比分析了6种不同液冷板布置位置下电芯模块高倍率放电时电芯模组温度云图、最高温度、最大温差以及平均温度等数据,确定了方案5具有最佳散热效果,为电池热管理开发研究提供了重要的参考价值。
参考文献:
[1]朱浩,刘云峰,赵策. 锂离子电池参数辨识与 SOC 估算研究[J].湖南大学学报(自然科学版),2014.
[2]LIU R, CHEN J, XUN J, et al. Numerical investigation of thermal behaviors in lithium-ionbattery stack discharge [J]. Applied Energy, 2014.
[3]Chen D,Jiang J,Kim G H,et al. Comparison of different cooling methods for lithium ion battery cell[J]. Appl.therm. Eng.,2016.
[4]郭建忠, 罗仁宏,王之丰,等. 商用车发动机舱热管理一维/三维联合仿真与试验[J]. 中国机械工程,2016.
[5]罗仁宏,郭建忠,胡溧,等. 某商用车发动机舱散热性能的提升与试验研究[J].制造业自动化,2015.
[6]YOUNG SAM C. China to give stimulus for development of electric vehicles[N]. Bloomberg News,2012.
[7]徐晓明.电动汽车冷却系统热流场的协同分析与液冷关键问题研究[D]. 南京:南京航空航天大学,2012.